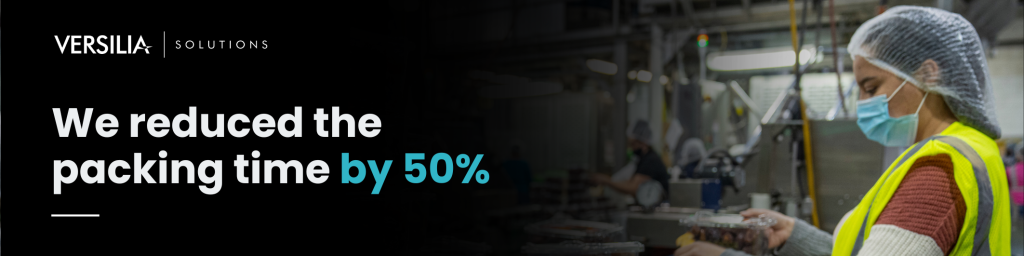
The challenge
When quoted costs for Last Mile Services at Vienna Airport far exceeded the expectations of our airline customer, it became clear that the traditional supplier model wasn’t viable. The solution was to create a new catering unit ourselves – one that could deliver the required performance at a significantly lower cost.
Our approach
We secured a partnership with an existing catering facility at Vienna Airport, renting space that allowed us to operate independently within a shared environment. From there, we built a ground operation from the ground up – recruiting and training a team of six packers to cover daily operational requirements. To ensure the unit ran efficiently from day one, we applied Lean Six Sigma methodology, as well as the principles of 5S and the Eight Wastes. These guided improvements to packing times, staff scheduling, warehouse layout and stock control, helping us to eliminate inefficiencies and reduce waste at every stage of the process.
The outcome
By applying Lean principles, we successfully halved packing time and optimised use of both labour and physical space. The Vienna unit is now fully flexible to accommodate last-minute changes – whether that’s aircraft swaps, unscheduled flights or late crew requests – while maintaining full operational performance.
Most importantly, the solution delivered an estimated €350,000 annual saving for our customer – around 40% lower than the original provider quotes – with no compromise on quality or reliability.
Before/After
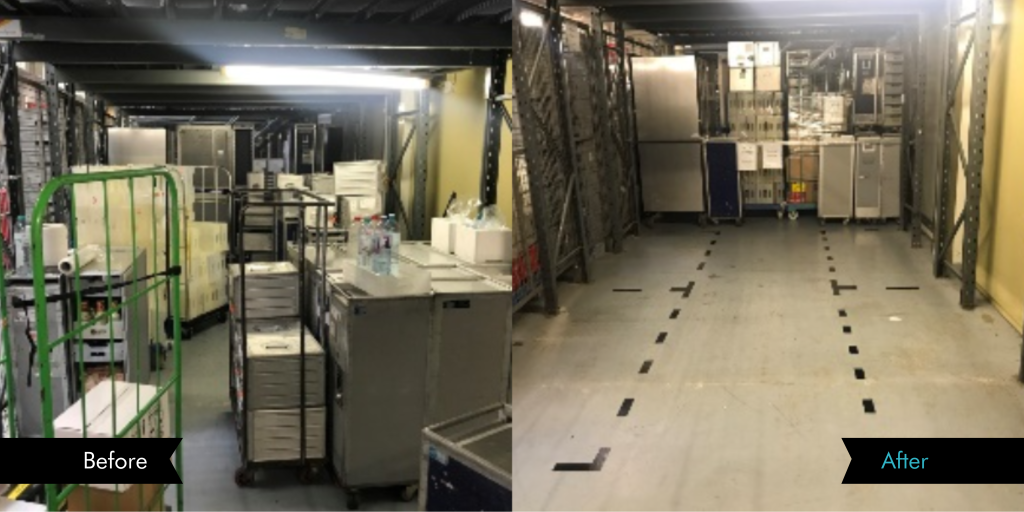
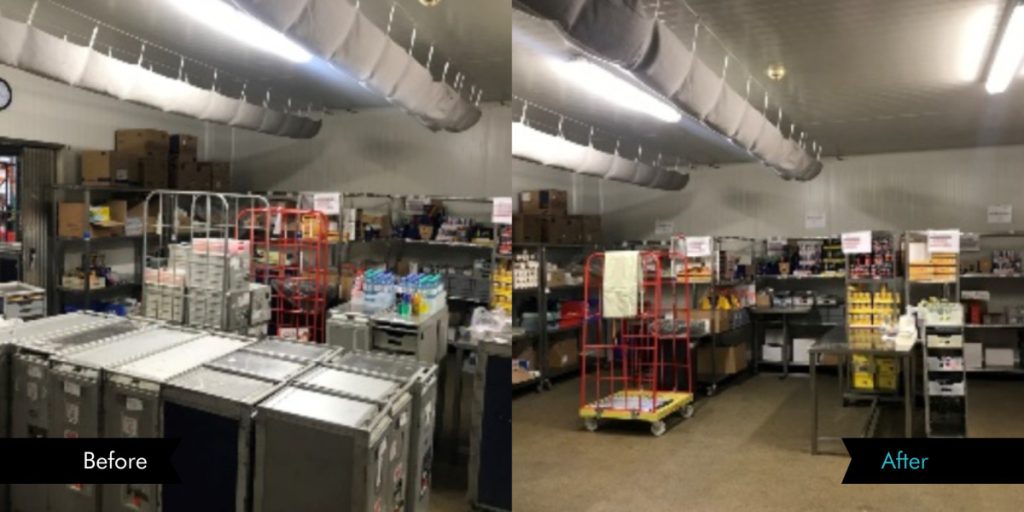
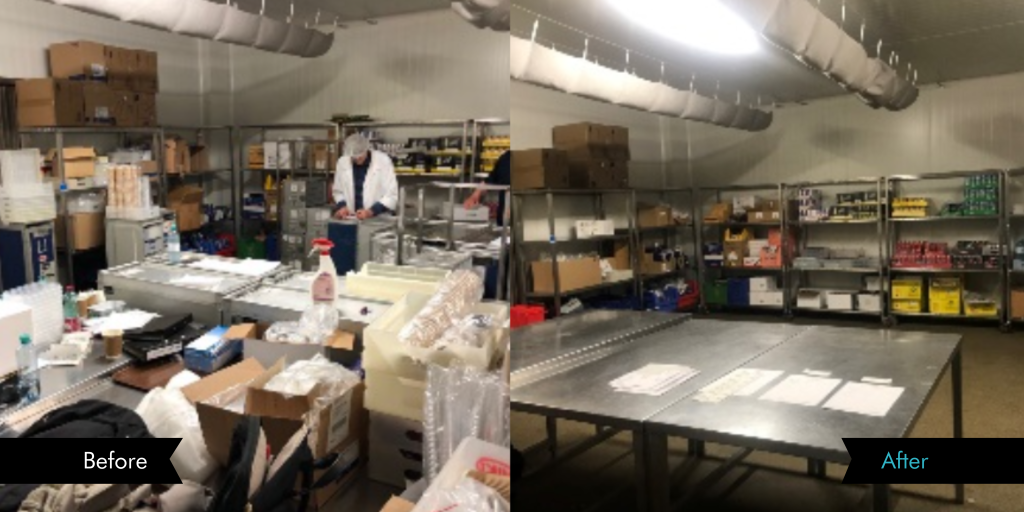